OLAB, an Italian refrigeration component manufacturer, has developed what it calls a “revolutionary” stainless-steel flanged ball valve for high-pressure CO2 (R744) systems that addresses the leakage issues commonly associated with traditional ball valves and that the company describes as “future-proof.”
First presented last October at the Chillventa trade show in Nuremberg, Germany, then showcased February 26–March 2 at the EuroShop trade show in Düsseldorf, Germany, OLAB’s new patent-pending Series Revolution ball valve has been designed to eliminate leaks in transcritical CO2 systems for commercial and industrial installations, explained Battista Guerini, OLAB Refrigeration Sales Manager, in an interview at OLAB’s EuroShop booth. Air Ram Cylinder

The Series Revolution ball valve is rated for 150bar (2,176psi), with a safety factor of three (450bar/6,527psi). It accommodates piping from 10 to 60.3mm (0.4 to 2.4in) in diameter with flow rates of 4 to 175m3/h (141 to 6,180ft3), at temperatures ranging from -50 to 150°C (-58 to 302°F).
Founded in 1988, OLAB puts a “strong emphasis on sustainability,” said Guerini.
“OLAB’s philosophy is built on four key principles: history, passion, people and technology,” he added. “This innovative spirit, backed by decades of know-how, has enabled the company to develop an impressive range of cutting-edge solenoid valves, valves and fittings specifically designed for CO2 systems.”
He said the Series Revolution ball valve “promises to be a game-changer in the world of sustainable refrigeration.”
It will do this by dint of its design, which avoids the need for TIG welding in the ball-valve body. Welding of tubes onto the flange (made of stainless steel or brass) on both sides of the valve is initially done at two points with the flange connected to the valve to ensure a proper fit. Then the flanges are disconnected and the welding is completed; each welded flange is then attached to the ball valve with Class A2 stainless steel screws in a very simple operation. Two O-Rings are used between the valve and the flanges to ensure the seal.
“Leaks in brass ball valves for refrigeration systems are attributable to welding on the ball-valve body, and even in traditional stainless steel versions there is a risk of damaging the seals by welding the pipes directly to the valve,” Guerini explained. The Series Revolution ball-valve body is weld-free and “solves all of the problems associated with traditional ball valves with welded or threaded ODS [oxide-dispersion-strengthened alloy] connections,” says OLAB in its product brochure. “The welding of the pipes on the detached flanges preserves the integrity of the seals,” added Guerini.
“Welds on the bodies of traditional brass ball valves can be dangerous at high pressures,” observed Guerini, “At 50 bar it works, but at 80 to 130 bar you have to be very lucky” to prevent small cracks from eventually forming. “That is why OLAB has put all its know-how and high-quality technology into developing such a revolutionary solution.”
In addition, this design allows for the “interchangeability of the flanges to change the type of device connections without having to change the entire valve,” says the product brochure. It also enables the valve body to be easily replaced “without having to cut the connecting pipes.”
“Replacement and maintenance are very easy,” noted Guerini. Moreover, the valve body can be updated and reused rather than discarded; this is an ecologically friendly practice that also saves the end user money, he added.
Guerini attributes the development of the new ball valve to OLAB’s business philosophy. “When you understand deeply what the problem of your customer is, and you have the technology we have, and the passion for what we do, and the will to do something different, you can do it,” he said.
In a statement from OLAB, the company emphasizes “its commitment to innovation and excellence by investing annually in cutting-edge technologies specifically tailored for the company. This investment allows OLAB to continuously improve its production processes and the quality of the innovations developed by their passionate and experienced R&D department. What sets the products of OLAB apart is that they are not only strictly made in Italy, but also 100% made in OLAB, ensuring the highest levels of quality and craftsmanship. The dedication of OLAB to its C=customers is evident in its comprehensive 360-degree approach, which encompasses every aspect of the customer experience, from product design to post-sales support.”
“With the commitment of OLAB to sustainability and innovation, the future of sustainable refrigeration is looking brighter and greener than ever,” the company said.
“Leaks in brass ball valves for refrigeration systems are attributable to welding on the ball-valve body.”
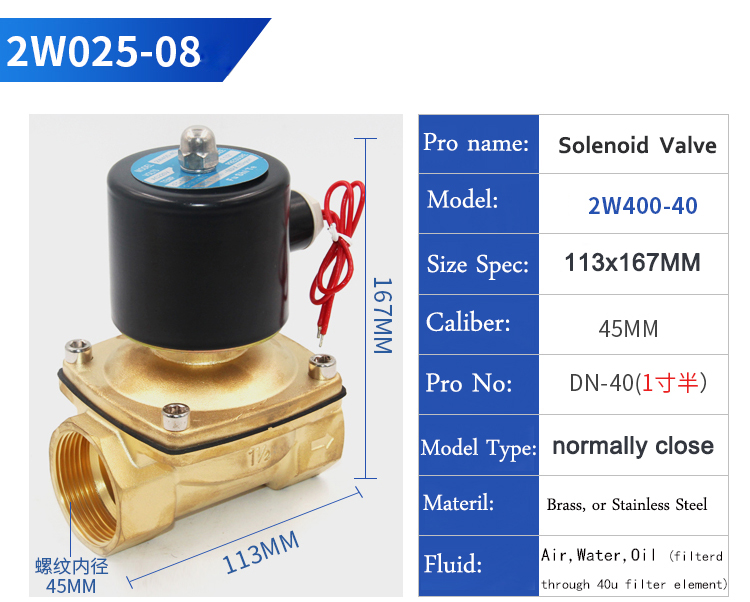
Double Rod Air Cylinder Username or email address *